As the leading manufacturer and exporter of weighing equipment, A&D Inspection brings you this expert-approved guide on finding the right checkweighing equipment for your facility.
Checkweighers are important in ensuring that all products in the production line are weighed accurately and conform to industry packaging standards. Without checkweighers, many companies would have to bank on unreliable weighing processes that could expose their business to potential risks including profit loss and expensive penalties. Distributing incorrectly weighed products comes at a cost; several industries impose hefty fines for underweight products and overweight products often result in high product giveaway and profit loss.
Industries such as food, beverage, pharmaceuticals, transport and logistics all utilise checkweighers to achieve fast production while maintaining great precision.
However, to yield the best results and optimise profits, business owners should realise that several factors play into successful checkweighing, including product types and sizes, environmental conditions, and other variables should be properly gauged as these affect the accuracy of checkweighing. Read on to find out more!
Consideration #1: Selecting the right checkweighing system

Defining your specific operational needs is crucial when buying a checkweigher. Once you have your production goals in mind, it becomes easy to figure out the right checkweighing system that would be relevant to your requirements.
Checkweighing systems can be classified into two types: Static and Dynamic.
- Static Checkweighers or Manual Checkweighers, measure the weight of items that are not in motion and are used to spot-check a small percentage of products. They also determine target weights for Dynamic Checkweighers and aid in net weight and tare weight sample tests to ensure compliance with industry regulations. Another common use for static checkweighers is found in rework stations of dynamic checkweighers to help aid in making the underweight product compliant.
- Dynamic Checkweighers or In-Motion Checkweighers, on the other hand, weigh moving products automatically and function without manual input from users. Unlike Static Checkweighers, these units are equipped with automated removal devices like pneumatic pusher arms or air-jets to dispose off-weight products.
Consideration #2: Product characteristics
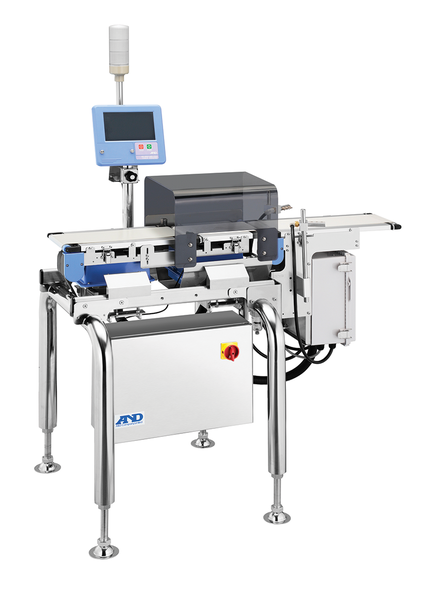
Consider the characteristics of the product or items that will be handled by the checkweigher.
Some checkweighers are designed specifically for certain types of packages like cases, cans, bags, and cartons. Other items like tall bottles may also require special checkweighing systems as these can be top-heavy and unstable.
Common package types weighed include the following:
- Boxes or cartons
- Bottles or cans
- Buckets
- Pouches
- Bags
- Tubes
For companies that frequently handle products such as these, check out A&D Inspection’s Checkweigher.
Depending on the general size and weight of these products, you can determine the appropriate size of your checkweigher in terms of belt dimensions and the right load cell weighing range. Other product characteristics such as height, shape and footprint also affect the overall precision of checkweighers.
Consideration #3: Environmental conditions
The accuracy and efficiency of checkweighing will be highly affected if environmental conditions aren’t properly checked.
Ask yourself the following questions when purchasing checkweighers:
- Is my workplace under excessive temperature?
- Are my checkweighers in the vicinity of debris and dust?
- Will I put my unit in location exposed to ‘noise’ or unwanted signals?
- How is the air current in the room?
- Are my units shielded from electrical noise?
- If my operating area can be kept clean or has corrosive elements in it? For example, chlorinated chemical or salt.
- Is there moisture or excessive condensation on or around the items to be weighed?
- Are my units protected against dust and water penetration?
Depending on your assessment, you can determine the features of checkweighers appropriate for you. For example, if the checkweigher will more likely be exposed to an environment with moisture or extreme condensation, you may need units with protection against solid and water ingress. There are several checkweighers with high resolution scales suitable for wet environments. Browse through the Checkweighing systems at A&D Inspection for more information.
Debris and dust falling on and around the scale can negate the tare setting on the checkweigher. You may need to re-zero the scale regularly if the debris constantly builds on platforms. Putting a cover on the scale which keeps the area around the checkweigher clean and avoids dust formation, or getting dust resistant scales like A&D Inspection’s Checkweigher models is the best possible solution.
Consideration #4: Software and connectivity
Choosing the right checkweighing system will positively impact both your revenue and productivity. There are available checkweighers that are bundled with on board software options and connectivity to ensure the best possible results.
Certain checkweighers like the A&D Checkweigher have various summary data tools including Histograms (frequency of defects), X charts and R charts which can be output to a printer via Ethernet or USB.
Consideration #5: Checkweighing combination systems
Some checkweighers come available with combination systems and can be specified to be integrated with either metal detection systems, X-ray systems, or vision inspection systems. These checkweighing solutions have a more compact area, which saves space in the production lines, and minimizes operation errors while providing faster product transitions. Also, combination systems reduce maintenance time and cost by granting easier line integration.
For example, businesses within the food industry face the challenge of clearing their products of contaminants or foreign objects while keeping accurate product weighing results. A checkweigher combined with a metal detector would be a good way to get a good return on investment in little time. Looking for a good combination checkweighing system? Check A&D Inspection’s Checkweighing System.
Consideration #6: Certifications and regulations

Keep in mind that for the industries that offer pre-packed goods or exact weight packs, the use of reliable systems is pertinent to the success of any checkweighing program.
Our checkweighers feature USDA certified food grade belts that are suitable for direct food contact. Our system also features a four level user access that works seamlessly with our built in audit trial. This means that each line worker can have a personal login that records the changes applied to the affected product. For quality assurance supervisor this feature eliminates guess work and further contributes to the integrity of the food safety program.
Consideration #7: Choosing the right partner
A&D has been providing industry-leading precision weighing and measurement equipment across the world for over 40 years. At A&D Inspection, you can rest easy knowing that each piece of equipment passes through the highest of quality standards at ISO 9001 certified facilities.
Our systems offer ease in terms of maintenance and uptime while offering the operator simplicity through our touchscreen display. Our systems feature modular design which positions A&D as a leader in our ability to deliver products at record pace.
Click on the links to view A&D Inspection’s complete line of Checkweighing Scales and Accessories.